Polycarbonate Nameplates
Durable Polycarbonate Nameplates
Do you need polycarbonate nameplates for a specific application? If so, you need an experienced manufacturer who will work with you to meet the highly specific end-product you require.
Hallmark Nameplate offers polycarbonate carbonate nameplates suitable for nearly all applications. Polycarbonate products are preferred due to their durability & flexibility in use. Our options include LEXAN®, AUTOFLEX®, & more. We are a manufacturer with 35+ years of meeting clients' custom nameplate needs.
Customizable Polycarbonate Options
We will work with you to create a fully customized solution to fit your business's exact needs and standards. We can customize each Polycarbonate Nameplate down to the most intricate detail. We will pinpoint the exact colors, texture, and finish to develop nameplates that exceed your expectations and fulfill your specific requirements.
This includes the very top layer of the product. Since these are custom products, our customers can approach our team with specific requests or materials that they need us to use to abide by their industry requirements.
However, we are also approached by those looking for guidance, who may be seeking direction or suggestions that will best suit their needs.
The most popular solution is Polycarbonate Overlays and Nameplates.
Why Use Polycarbonate Nameplates?
Compared to traditional overlays and nameplates, Polycarbonate Overlays and Polycarbonate Nameplates can be manufactured with transparent features and give you the option to choose from various textured finishes which provides maximum durability. The finish is ideal for highly detailed printing.
Polycarbonate resin is a thermoplastic material that’s transparent, strong, impact-resistant, and temperature resistant. It provides exceptional optical clarity, color reproduction, depth effect, graphic design flexibility, printability, and dimensional stability.
Polycarbonate is an eco-friendly material that is flame retardant, UV resistant, and compliant with FDA and USP regulations. The environment that your overlay or nameplate will live in will help to make a lot of the decisions when it comes to the development. Hallmark Nameplate will help you through every step of the production.
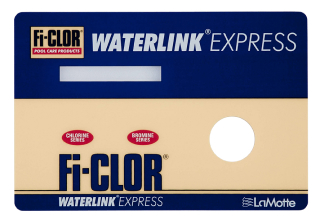
Advantages of Polycarbonate Finishes
Why could a Polycarbonate finish be the right material for you? This specific finish protects against harsh conditions both indoors and outdoors. Polycarbonate overlays and nameplates will be protected from UV rays, extreme temperatures, and everyday operation. It is resistant to scratches, corrosion, chemical abrasion, and water without damaging the material.
The goal is to maintain the appearance, longevity, legibility, and functionality of the overlay in its environment. The printing process is normally done on the underside of the plastic to permanently protect the graphic and ensure durability. Your labels need to be made to last and brand your product for a lifetime.
How Different Industries Use Polycarbonate Overlays
You’ll most commonly see polycarbonate overlays and nameplates in the electronic industry, but they are also found in aerospace, automotive, computers, and medical fields.
Found on:
- Appliances
- Control systems
- Instrumentation
- Military equipment
- Computer hardware
- Airlines
- Industrial equipment
Used for:
- Warning labels
- Keypad switches
- Instruction labels
- Nameplates
- Logos
- Product identification
Your facility and equipment may require materials with precise specifications, certifications, or inspection procedures.
We are UL certified, RoHS, and ITAR compliant and a 3M Preferred Converter. Other certifications include ISO 13485:2016, ISO 9001:2015, and GPI.
Customize Your Polycarbonate Overlays & Nameplates
We will walk you through the development process to ensure you select the materials and designs that are best for your business’s specific needs.
- 8010 Lexan, Clear
- 8010V Lexan, Clear
- 8A13V Lexan, Matte
- 8A35 Lexan, Velvet (5-25 mils)
- 8B35 Lexan, Velvet (3-20 mils)
- 8B35E Lexan, Velvet
- 8B35F Lexan, Velvet
- 8B35V Lexan, Velvet
- 8B35FV Lexan, Velvet
- 8B36 Lexan, Suede
- AutoFlex PC
- Covestro Makrofol® DE 1-1 000000 Clear Polycarbonate
- Covestro Makrofol DE 7-2 000000 Polycarbonate
- FR60 Lexan, Polished
- FR63 Lexan, Matte
- FR65 Lexan, Velvet
- FR66 Lexan, Suede
- FR83 Lexan, Matte
- FR700 Lexan, Velvet
- HPXXS Lexan
- HPXXW Lexan
- Marnot® XL Hardcoat Clear Polycarbonate (Marnot XL Polycarbonate)
- RowTec® Polycarbonate
Autoflex®
Autoflex® PC from MacDermid Autotype is a hard-coated polycarbonate that provides exceptional clarity, low yellowness, low haze, and both chemical and scratch resistance. Autoflex is resistant to alcohols, dilute acids and alkalis, petrol and diesel, most household cleaning agents, and certain aggressive organic solvents. It also has a consistent gloss or anti-glare hard coat surfaces.
Autoflex PC Gloss G180, G250, G380, G480, G640, G750
Gloss finish; 180, 250, 380, 480, 640, 750 microns
Autoflex PC Antiglare A180, A250, A380, A480, A640, A750
Antiglare finish; 180, 250, 380, 480, 640, 750 microns
Lexan
Lexan 8010 and Lexan 8010V clear polycarbonate films offer excellent clarity in every thickness, high heat resistance and dimensional stability. It’s one of the world’s most rugged polymers. Lexan 8010 film has a high gloss finish and meets requirements for UV stability. Lexan 8010V has the same properties, plus exceptional dimensional stability for applications that require UL94 flammability performance.
Lexan 8A13, 8A35, 8A37, 8B35, and 8B36 are transparent polycarbonate films, available in different textures. They provide high-temperature resistance, dimensional stability, and good printability, making them suitable for high-performance labels and overlays. The velvet texture is mar-resistant and can be used over LEDs.
Matte 8A13-112 (7-25 mils)
Velvet 8A35-112 (5-25 mils)
Brushed 8A37-112 (10-20 mils)
Velvet 8B35-112 (3-20 mils)
Suede 8B36-112 (10-20 mils)
Lexan 8A13V film is a matte finished transparent polycarbonate film, with all the features of 8A13 plus UL94 flammability performance
Lexan 8B35E transparent polycarbonate film has a velvet finish. Features include exceptional clarity, resistance against high heat, and excellent dimensional stability for all material thicknesses. Its low gloss finish makes it perfect for back-lit dials, overlays, dead-front graphics, and display protection.
Lexan 8B35F transparent polycarbonate film, with a velvet finish, is designed to eliminate pinholes for backlit uses. It offers heat resistance, clarity, and dimensional stability, plus a smooth surface.
Lexan 8B35V is polycarbonate film with a velvet finish, with the same features of 8B35 in addition to meeting UL94 flammability requirements.
Lexan 8B35FV film is velvet finished transparent polycarbonate, with the same properties as 8B35F, with UL94 flammability characteristics.
Note: The following Lexan film grades now meet UL94 - VTM-2 / V-2 ratings: 8010 (30mil), 8A13F (20mil), 8A35 (7mil, 20mil), 8B35 (7mil, 15mil, 20mil), and 8B35F (15mil through 30mil), with the same specifications for gauge/width tolerance, gloss, surface texture, and cosmetic variables. V grades have been discontinued.
Lexan HPXXS Series UV coated graphic film is high performance with very good abrasion and chemical resistance. It’s highly durable and easily printed, with coating and texture adhesion, even with exposure to household cleaners.
Lexan HPXXW Series high-performance coated film offers very good resistance to abrasion, chemicals, and UV. It has a special coating that’s resistant to hazing and yellowing in bright sunlight. These qualities make HPXXW recommended for outdoor graphic uses such as warning labels and marine graphics.
Lexan FRXX is a flame-retardant, clear, thin-gauge polycarbonate film, available in different finishes. Its UL94 V-0 listing meets the strictest requirements for various electronic, electrical and transportation uses. This material supports die-cutting, thermoforming, and hydroforming, and is excellent for backlit aircraft in-flight displays and panels, among other applications.
Lexan FR60 – polished
Lexan FR63 – matte
Lexan FR65 – velvet
Lexan FR66 – suede
Lexan FR83 – transparent matte
Lexan FR700 black, velvet flame-retardant polycarbonate film is dimensionally stable at high temperatures and has a high flammability rating. It also has a UL94 V-0 listing and superior mechanical properties
Marnot XL
Marnot XL Clear Hardcoated Polycarbonate offers the appearance of a clear gloss material with high chemical, scratch, and abrasion resistance. This makes it appropriate for appliance overlays, nameplates, and lenses.
RowTec®
RowTec® Polycarbonate films are recommended for applications that require thermal, optical, electrical, and mechanical characteristics.
They’re available with different textures and thicknesses and provide clarity, impact resistance, dimensional stability, and dielectric properties. RowTec polycarbonate is used for applications like labels, backlit displays, dial indicators, instrument panel overlays, graphic panels, and scales. Thicknesses range from 0.002” – 0.040”, and in gloss, velvet, matte, and suede.
RowTec – Standard Polycarbonate Film
RowTec HC – a high-abrasion and chemically resistant coated film
RowTec RT – with PreLume® Light Reflection Technology for whiter, brighter graphics
RowTec V – meets UL94 VTM-2 at 0.005” - 0.010”
With selective textures and adhesives, different parts of the overlay and nameplate are treated in different ways. Usually, the finished nameplate has the finish/texture of the base material and the graphics are reverse printed on the untextured underside of the material.
Textures
We can apply (print or laminate) finishes/textures on the top side, covering the entire surface, or print only in certain areas selectively. For example, we can take a glossy polyester nameplate and print a selective velvet texture over everything except for the company logo graphic and text. This makes the logo “pop out” from the background.
Adhesives
The adhesive is usually rolled on and covers the entire underside of the nameplate. It can have holes selectively cut in it for transparent windows. Windows are areas with no printing which may or may not have adhesive.
Polycarbonate Overlays & Nameplates at Hallmark Nameplate
Whether your product is in its existing or early stage of development, you can rest assured that Hallmark Nameplate will assist you with your design and any other requirements you may have.
Fill out a form on our contact page today to get started!